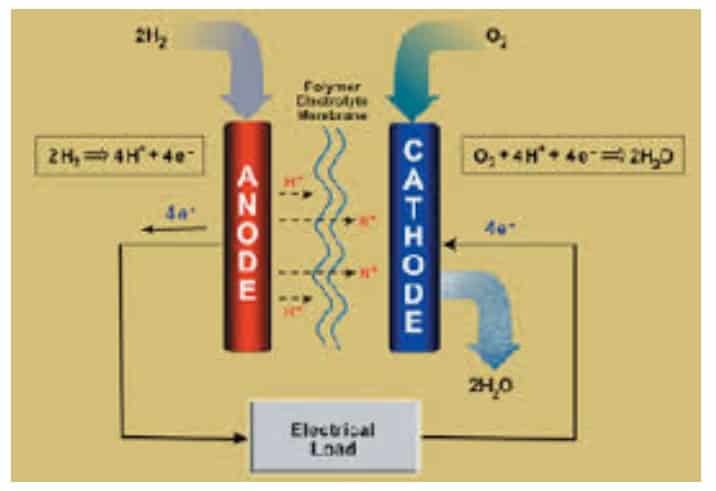
…by Jeff Smith, VT Science Editor
Fuel cells, Cold Fusion and Low Energy Nuclear Reactions are all Catalytic process or Catalytic Converters. They all do the same thing but in different ways. Cold Fusion research is a spin off of Fuel Cell technology research started by NASA in the 1960’s. It is nothing but a thermal fuel cell with no electrical output. All fuel cells produce excess heat due to a catalytic process that is either molecular or atomic in nature. Therefore Cold Fusion is a scam. While fuel cells are efficient relative to combustion engines, they are not as efficient as batteries.
A fuel cell is a device that converts the chemical energy from a fuel into electricity through a chemical reaction with oxygen or another oxidizing agent. Hydrogen produced from the steam methane reforming of natural gas is the most common fuel, but for greater efficiency hydrocarbons can be used directly such as natural gas and alcohols like methanol.
Fuel cells are different from batteries in that they require a continuous source of fuel and oxygen/air to sustain the chemical reaction whereas in a battery the chemicals present in the battery react with each other to generate an electromotive force (emf). Fuel cells can produce electricity continuously for as long as these inputs are supplied.
The first ones were invented in 1838. The first commercial use came more than a century later in NASA space programs to generate power for probes, satellites and space capsules. Since then, fuel cells have been used in many other applications. They are used for primary and backup power for commercial, industrial and residential buildings and in remote or inaccessible areas. They are also used to power fuel-cell vehicles, including forklifts, automobiles, buses, boats, motorcycles and submarines.
There are many types of fuel cells, but they all consist of an anode, a cathode and an electrolyte that allows charges to move between the two sides of the fuel cell. Electrons are drawn from the anode to the cathode through an external circuit, producing direct current electricity. As the main difference among fuel cell types is the electrolyte, fuel cells are classified by the type of electrolyte they use followed by the difference in startup time ranging from 1 sec for PEMFC to 10 min for SOFC.
Fuel cells come in a variety of sizes. Individual fuel cells produce relatively small electrical potentials, about 0.7 volts, so cells are “stacked”, or placed in series, to increase the voltage and meet an application’s requirements. In addition to electricity, fuel cells produce water, heat and, depending on the fuel source, very small amounts of nitrogen dioxide and other emissions. The energy efficiency of a fuel cell is generally between 40–60%, or up to 85% efficient in cogeneration if waste heat is captured for use.
_________________________
History
The first references to hydrogen fuel cells appeared in 1838. In a letter dated October 1838 but published in the December 1838 edition of The London and Edinburgh Philosophical Magazine and Journal of Science, Welsh physicist and barrister William Grove wrote about the development of his first crude fuel cells. He used a combination of sheet iron, copper and porcelain plates, and a solution of sulphate of copper and dilute acid.
In a letter to the same publication written in December 1838 but published in June 1839, German physicist Christian Friedrich Schönbein discussed the first crude fuel cell that he had invented. His letter discussed current generated from hydrogen and oxygen dissolved in water. Grove later sketched his design, in 1842, in the same journal. The fuel cell he made used similar materials to today’s phosphoric-acid fuel cell.
In 1939, British engineer Francis Thomas Bacon successfully developed a 5 kW stationary fuel cell. In 1955, W. Thomas Grubb, a chemist working for the General Electric Company, further modified the original fuel cell design by using a sulphonated polystyrene ion-exchange membrane as the electrolyte. Three years later another GE chemist, Leonard Niedrach, devised a way of depositing platinum onto the membrane, which served as catalyst for the necessary hydrogen oxidation and oxygen reduction reactions.
This became known as the “Grubb-Niedrach fuel cell”. GE went on to develop this technology with NASA and McDonnell Aircraft, leading to its use during Project Gemini. This was the first commercial use of a fuel cell. In 1959, a team led by Harry Ihrig built a 15 kW fuel cell tractor for Allis-Chalmers, which was demonstrated across the U.S. at state fairs. This system used potassium hydroxide as the electrolyte and compressed hydrogen and oxygen as the reactants.
Later in 1959, Bacon and his colleagues demonstrated a practical five-kilowatt unit capable of powering a welding machine. In the 1960s, Pratt and Whitney licensed Bacon’s U.S. patents for use in the U.S. space program to supply electricity and drinking water (hydrogen and oxygen being readily available from the spacecraft tanks). In 1991, the first hydrogen fuel cell automobile was developed by Roger Billings.
UTC Power was the first company to manufacture and commercialize a large, stationary fuel cell system for use as a co-generation power plant in hospitals, universities and large office buildings. UTC Power continues to be the sole supplier of fuel cells to NASA for use in space vehicles, having supplied fuel cells for the Apollo missions, and the Space Shuttle program, and is developing fuel cells for cell phone towers and other applications.
_________________________________
Types of fuel cells; design
Fuel cells come in many varieties; however, they all work in the same general manner. They are made up of three adjacent segments: the anode, the electrolyte, and the cathode. Two chemical reactions occur at the interfaces of the three different segments. The net result of the two reactions is that fuel is consumed, water or carbon dioxide is created, and an electric current is created, which can be used to power electrical devices, normally referred to as the load.
At the anode a catalyst oxidizes the fuel, usually hydrogen, turning the fuel into a positively charged ion and a negatively charged electron. The electrolyte is a substance specifically designed so ions can pass through it, but the electrons cannot. The freed electrons travel through a wire creating the electric current. The ions travel through the electrolyte to the cathode.
Once reaching the cathode, the ions are reunited with the electrons and the two react with a third chemical, usually oxygen, to create water or carbon dioxide. This is a catalytic reaction with hydrogen and oxygen. In Cold Fusion cells the same process is used to create excess heat from the catalytic reaction but no external electricity is produced for use, only the excess thermal heat is extracted from the cell for use.
The most important design features in a fuel cell are:
- The electrolyte substance. The electrolyte substance usually defines the type of fuel cell.
- The fuel that is used. The most common fuel is hydrogen.
- The anode catalyst breaks down the fuel into electrons and ions. The anode catalyst is usually made up of very fine platinum powder.
- The cathode catalyst turns the ions into the waste chemicals like water or carbon dioxide. The cathode catalyst is often made up of nickel but it can also be a nano material-based catalyst.
A typical fuel cell produces a voltage from 0.6 V to 0.7 V at full rated load. Voltage decreases as current increases, due to several factors:
- Activation loss
- Ohmic loss (voltage drop due to resistance of the cell components and interconnections)
- Mass transport loss (depletion of reactants at catalyst sites under high loads, causing rapid loss of voltage).
To deliver the desired amount of energy, the fuel cells can be combined in series to yield higher voltage, and in parallel to allow a higher current to be supplied. Such a design is called a fuel cell stack. The cell surface area can also be increased, to allow higher current from each cell. Within the stack, reactant gases must be distributed uniformly over each of the cells to maximize the power output.
____________________________
Proton exchange membrane fuel cells (PEMFCs)
In the archetypical hydrogen–oxide proton exchange membrane fuel cell design, a proton-conducting polymer membrane (the electrolyte) separates the anode and cathode sides. This was called a “solid polymer electrolyte fuel cell” (SPEFC) in the early 1970s, before the proton exchange mechanism was well-understood. (Notice that the synonyms “polymer electrolyte membrane” and “proton exchange mechanism” result in the same acronym.)
On the anode side, hydrogen diffuses to the anode catalyst where it later dissociates into protons and electrons. These protons often react with oxidants causing them to become what are commonly referred to as multi-facilitated proton membranes. The protons are conducted through the membrane to the cathode, but the electrons are forced to travel in an external circuit (supplying power) because the membrane is electrically insulating. On the cathode catalyst, oxygen molecules react with the electrons (which have traveled through the external circuit) and protons to form water.
In addition to this pure hydrogen type, there are hydrocarbon fuels for fuel cells, including diesel, methanol and chemical hydrides. The waste products with these types of fuel are carbon dioxide and water, when hydrogen is used the CO2 is released when methane from natural gas is combined with steam in a process called steam methane reforming to produce the hydrogen, this can take place in a different location to the fuel cell potentially allowing the hydrogen fuel cell to be used indoors for example in fork lifts.
The different components of a PEMFC are;
- bipolar plates
- electrodes
- catalyst
- membrane
The materials used for different parts of the fuel cells differ by type. The bipolar plates may be made of different types of materials, such as, metal, coated metal, graphite, flexible graphite, C–C composite, carbon–polymer composites etc. The membrane electrode assembly (MEA) is referred as the heart of the PEMFC and is usually made of a proton exchange membrane sandwiched between two catalyst-coated carbon papers. Platinum and/or similar type of noble metals are usually used as the catalyst for PEMFC. The electrolyte could be a polymer membrane.
__________________________
Proton exchange membrane fuel cell design issues
- Costs. In 2013, the Department of Energy estimated that 80-kW automotive fuel cell system costs of US$67 per kilowatt could be achieved, assuming volume production of 100,000 automotive units per year and US$55 per kilowatt could be achieved, assuming volume production of 500,000 units per year. Many companies are working on techniques to reduce cost in a variety of ways including reducing the amount of platinum needed in each individual cell. 30% reduction (1 mg/cm² to 0.7 mg/cm²) in platinum usage without reduction in performance. A 2011 published study documented the first metal-free electro catalyst using relatively inexpensive doped carbon nanotubes, which are less than 1% the cost of platinum and are of equal or superior performance.
- Water and air management (in PEMFCs). In this type of fuel cell, the membrane must be hydrated, requiring water to be evaporated at precisely the same rate that it is produced. If water is evaporated too quickly, the membrane dries, resistance across it increases, and eventually it will crack, creating a gas “short circuit” where hydrogen and oxygen combine directly, generating heat that will damage the fuel cell. If the water is evaporated too slowly, the electrodes will flood, preventing the reactants from reaching the catalyst and stopping the reaction. Methods to manage water in cells are being developed like electroosmotic pumps focusing on flow control. Just as in a combustion engine, a steady ratio between the reactant and oxygen is necessary to keep the fuel cell operating efficiently.
- Temperature management. The same temperature must be maintained throughout the cell in order to prevent destruction of the cell through thermal loading. This is particularly challenging as the 2H2 + O2 -> 2H2O reaction is highly exothermic, so a large quantity of heat is generated within the fuel cell.
- Durability, service life, and special requirements for some type of cells. Stationary fuel cell applications typically require more than 40,000 hours of reliable operation at a temperature of −35 °C to 40 °C (−31 °F to 104 °F), while automotive fuel cells require a 5,000-hour lifespan (the equivalent of 240,000 km (150,000 mi)) under extreme temperatures. Current service life is 7,300 hours under cycling conditions. Automotive engines must also be able to start reliably at −30 °C (−22 °F) and have a high power-to-volume ratio (typically 2.5 kW per liter).
- Limited carbon monoxide tolerance of some (non-PEDOT) cathodes.
___________________
Phosphoric acid fuel cell (PAFC)
Phosphoric acid fuel cells (PAFC) were first designed and introduced in 1961 by G. V. Elmore and H. A. Tanner. In these cells phosphoric acid is used as a non-conductive electrolyte to pass positive hydrogen ions from the anode to the cathode. These cells commonly work in temperatures of 150 to 200 degrees Celsius. This high temperature will cause heat and energy loss if the heat is not removed and used properly. This heat can be used to produce steam for air conditioning systems or any other thermal energy consuming system.
The efficiency of phosphoric acid fuel cells is from 40 to about 80%. Phosphoric acid, the electrolyte used in PAFCs, is a non-conductive liquid acid which forces electrons to travel from anode to cathode through an external electrical circuit. Since the hydrogen ion production rate on the anode is small, platinum is used as catalyst to increase this ionization rate. A key disadvantage of these cells is the use of an acidic electrolyte. This increases the corrosion or oxidation of components exposed to phosphoric acid.
___________________________________
High-temperature fuel cells
Solid oxide fuel cells (SOFCs) use a solid material, most commonly a ceramic material called yttria-stabilized zirconia (YSZ), as the electrolyte. Because SOFCs are made entirely of solid materials, they are not limited to the flat plane configuration of other types of fuel cells and are often designed as rolled tubes. They require high operating temperatures (800–1000 °C) and can be run on a variety of fuels including natural gas.
SOFCs are unique in that negatively charged oxygen ions travel from the cathode (positive side of the fuel cell) to the anode (negative side of the fuel cell) instead of positively charged hydrogen ions travelling from the anode to the cathode, as is the case in all other types of fuel cells. Oxygen gas is fed through the cathode, where it absorbs electrons to create oxygen ions.
The oxygen ions then travel through the electrolyte to react with hydrogen gas at the anode. The reaction at the anode produces electricity and water as by-products. Carbon dioxide may also be a by-product depending on the fuel, but the carbon emissions from an SOFC system are less than those from a fossil fuel combustion plant. The chemical reactions for the SOFC system can be expressed as follows:
- Anode Reaction: 2H2 + 2O2− → 2H2O + 4e−
- Cathode Reaction: O2 + 4e– → 2O2−
- Overall Cell Reaction: 2H2 + O2 → 2H2O
SOFC systems can run on fuels other than pure hydrogen gas. However, since hydrogen is necessary for the reactions listed above, the fuel selected must contain hydrogen atoms. For the fuel cell to operate, the fuel must be converted into pure hydrogen gas. SOFCs are capable of internally reforming light hydrocarbons such as methane (natural gas), propane and butane. These fuel cells are at an early stage of development.
Challenges exist in SOFC systems due to their high operating temperatures. One such challenge is the potential for carbon dust to build up on the anode, which slows down the internal reforming process. Research to address this “carbon coking” issue at the University of Pennsylvania has shown that the use of copper-based cermet (heat-resistant materials made of ceramic and metal) can reduce coking and the loss of performance.
Another disadvantage of SOFC systems is slow start-up time, making SOFCs less useful for mobile applications. Despite these disadvantages, a high operating temperature provides an advantage by removing the need for a precious metal catalyst like platinum, thereby reducing cost. Additionally, waste heat from SOFC systems may be captured and reused, increasing the theoretical overall efficiency to as high as 80%–85%.
The high operating temperature is largely due to the physical properties of the YSZ electrolyte. As temperature decreases, so does the ionic conductivity of YSZ. Therefore, to obtain optimum performance of the fuel cell, a high operating temperature is required. According to their website, Ceres Power, a UK SOFC fuel cell manufacturer, has developed a method of reducing the operating temperature of their SOFC system to 500–600 degrees Celsius.
They replaced the commonly used YSZ electrolyte with a CGO (cerium gadolinium oxide) electrolyte. The lower operating temperature allows them to use stainless steel instead of ceramic as the cell substrate, which reduces cost and start-up time of the system.
Molten carbonate fuel cells (MCFCs) require a high operating temperature, 650 °C (1,200 °F), similar to SOFCs. MCFCs use lithium potassium carbonate salt as an electrolyte, and this salt liquefies at high temperatures, allowing for the movement of charge within the cell – in this case, negative carbonate ions.
Like SOFCs, MCFCs are capable of converting fossil fuel to a hydrogen-rich gas in the anode, eliminating the need to produce hydrogen externally. The reforming process creates CO 2 emissions. MCFC-compatible fuels include natural gas, biogas and gas produced from coal. The hydrogen in the gas reacts with carbonate ions from the electrolyte to produce water, carbon dioxide, electrons and small amounts of other chemicals.
The electrons travel through an external circuit creating electricity and return to the cathode. There, oxygen from the air and carbon dioxide recycled from the anode react with the electrons to form carbonate ions that replenish the electrolyte, completing the circuit. The chemical reactions for an MCFC system can be expressed as follows:
- Anode Reaction: CO32− + H2 → H2O + CO2 + 2e−
- Cathode Reaction: CO2 + ½O2 + 2e− → CO32−
- Overall Cell Reaction: H2 + ½O2 → H2O
As with SOFCs, MCFC disadvantages include slow start-up times because of their high operating temperature. This makes MCFC systems not suitable for mobile applications, and this technology will most likely be used for stationary fuel cell purposes. The main challenge of MCFC technology is the cells’ short life span. The high-temperature and carbonate electrolyte lead to corrosion of the anode and cathode.
These factors accelerate the degradation of MCFC components, decreasing the durability and cell life. Researchers are addressing this problem by exploring corrosion-resistant materials for components as well as fuel cell designs that may increase cell life without decreasing performance.
MCFCs hold several advantages over other fuel cell technologies, including their resistance to impurities. They are not prone to “carbon coking”, which refers to carbon build-up on the anode that results in reduced performance by slowing down the internal fuel reforming process. Therefore, carbon-rich fuels like gases made from coal are compatible with the system.
The Department of Energy claims that coal, itself, might even be a fuel option in the future, assuming the system can be made resistant to impurities such as sulfur and particulates that result from converting coal into hydrogen. MCFCs also have relatively high efficiencies. They can reach a fuel-to-electricity efficiency of 50%, considerably higher than the 37–42% efficiency of a phosphoric acid fuel cell plant.
Comparison of fuel cell types
Fuel cell name | Electrolyte | Qualified power(W) | Working temperature (°C) | Efficiency(cell) | Efficiency (system) | Status | Cost (USD/W) |
---|---|---|---|---|---|---|---|
Metal hydride fuel cell | Aqueous alkaline solution | > -20 (50% Ppeak @ 0 °C) | Commercial / Research | ||||
Electro-galvanic fuel cell | Aqueous alkaline solution | < 40 | Commercial / Research | ||||
Direct formic acid fuel cell(DFAFC) | Polymer membrane (ionomer) | < 50 W | < 40 | Commercial / Research | |||
Zinc-air battery | Aqueous alkaline solution | < 40 | Mass production | ||||
Microbial fuel cell | Polymer membrane or humic acid | < 40 | Research | ||||
Upflow microbial fuel cell (UMFC) | < 40 | Research | |||||
Regenerative fuel cell | Polymer membrane (ionomer) | < 50 | Commercial / Research | ||||
Direct borohydride fuel cell | Aqueous alkaline solution | 70 | Commercial | ||||
Alkaline fuel cell | Aqueous alkaline solution | 10 – 100 kW | < 80 | 60–70% | 62% | Commercial / Research | |
Direct methanol fuel cell | Polymer membrane (ionomer) | 100 mW – 1 kW | 90–120 | 20–30% | 10–20% | Commercial / Research | 125 |
Reformed methanol fuel cell | Polymer membrane (ionomer) | 5 W – 100 kW | 250–300 (Reformer) 125–200 (PBI) | 50–60% | 25–40% | Commercial / Research | |
Direct-ethanol fuel cell | Polymer membrane (ionomer) | < 140 mW/cm² | > 25 ? 90–120 | Research | |||
Proton exchange membrane fuel cell | Polymer membrane (ionomer) | 100 W – 500 kW | 50–100 (Nafion) 125–220 (PBI) | 50–70% | 30–50% | Commercial / Research | 50–100 |
RFC – Redox | Liquid electrolytes with redox shuttle and polymer membrane (Ionomer) | 1 kW – 10 MW | Research | ||||
Phosphoric acid fuel cell | Molten phosphoric acid (H3PO4) | < 10 MW | 150-200 | 55% | 40% Co-Gen: 90% | Commercial / Research | 4–4.50 |
Solid acid fuel cell | H+-conducting oxyanion salt (solid acid) | 10 W – 1 kW | 200-300 | 55-60% | 40-45% | Commercial / Research | |
Molten carbonate fuel cell | Molten alkaline carbonate | 100 MW | 600–650 | 55% | 47% | Commercial / Research | |
Tubular solid oxide fuel cell(TSOFC) | O2--conducting ceramic oxide | < 100 MW | 850–1100 | 60–65% | 55–60% | Commercial / Research | |
Protonic ceramic fuel cell | H+-conducting ceramic oxide | 700 | Research | ||||
Direct carbon fuel cell | Several different | 700–850 | 80% | 70% | Commercial / Research | ||
Planar Solid oxide fuel cell | O2--conducting ceramic oxide | < 100 MW | 500–1100 | 60–65% | 55–60% | Commercial / Research | |
Enzymatic Biofuel Cells | Any that will not denature the enzyme | < 40 | Research | ||||
Magnesium-Air Fuel Cell | Salt water | −20 to 55 | 90% | Commercial / Research |
Glossary of Terms in table:
- Anode: The electrode at which oxidation (a loss of electrons) takes place. For fuel cells and other galvanic cells, the anode is the negative terminal; for electrolytic cells (where electrolysis occurs), the anode is the positive terminal.
- Aqueous solution: a: of, relating to, or resembling water b : made from, with, or by water.
- Catalyst: A chemical substance that increases the rate of a reaction without being consumed; after the reaction, it can potentially be recovered from the reaction mixture and is chemically unchanged. The catalyst lowers the activation energy required, allowing the reaction to proceed more quickly or at a lower temperature. In a fuel cell, the catalyst facilitates the reaction of oxygen and hydrogen. It is usually made of platinum powder very thinly coated onto carbon paper or cloth. The catalyst is rough and porous so the maximum surface area of the platinum can be exposed to the hydrogen or oxygen. The platinum-coated side of the catalyst faces the membrane in the fuel cell.
- Cathode: The electrode at which reduction (a gain of electrons) occurs. For fuel cells and other galvanic cells, the cathode is the positive terminal; for electrolytic cells (where electrolysis occurs), the cathode is the negative terminal.
- Electrolyte: A substance that conducts charged ions from one electrode to the other in a fuel cell, battery, or electrolyzer.
- Fuel Cell Stack: Individual fuel cells connected in a series. Fuel cells are stacked to increase voltage.
- Matrix: something within or from which something else originates, develops, or takes form.
- Membrane: The separating layer in a fuel cell that acts as electrolyte (an ion-exchanger) as well as a barrier film separating the gases in the anode and cathode compartments of the fuel cell.
- Molten Carbonate Fuel Cell (MCFC): A type of fuel cell that contains a molten carbonate electrolyte. Carbonate ions (CO32−) are transported from the cathode to the anode. Operating temperatures are typically near 650 °C.[46]
- Phosphoric acid fuel cell (PAFC): A type of fuel cell in which the electrolyte consists of concentrated phosphoric acid (H3PO4). Protons (H+) are transported from the anode to the cathode. The operating temperature range is generally 160–220 °C.
- Polymer Electrolyte Membrane (PEM): A fuel cell incorporating a solid polymer membrane used as its electrolyte. Protons (H+) are transported from the anode to the cathode. The operating temperature range is generally 60–100 °C.
- Solid Oxide Fuel Cell (SOFC): A type of fuel cell in which the electrolyte is a solid, nonporous metal oxide, typically zirconium oxide (ZrO2) treated with Y2O3, and O2− is transported from the cathode to the anode. Any CO in the reformate gas is oxidized to CO2 at the anode. Temperatures of operation are typically 800–1,000 °C.
- Solution: a: an act or the process by which a solid, liquid, or gaseous substance is homogeneously mixed with a liquid or sometimes a gas or solid, b : a homogeneous mixture formed by this process; especially : a single-phase liquid system, c : the condition of being dissolved
____________________________
Theoretical maximum efficiency
The energy efficiency of a system or device that converts energy is measured by the ratio of the amount of useful energy put out by the system (“output energy”) to the total amount of energy that is put in (“input energy”) or by useful output energy as a percentage of the total input energy. In the case of fuel cells, useful output energy is measured in electrical energy produced by the system. Input energy is the energy stored in the fuel. According to the U.S. Department of Energy, fuel cells are generally between 40–60% energy efficient. This is higher than some other systems for energy generation.
For example, the typical internal combustion engine of a car is about 25% energy efficient. In combined heat and power (CHP) systems, the heat produced by the fuel cell is captured and put to use, increasing the efficiency of the system to up to 85–90%.
The theoretical maximum efficiency of any type of power generation system is never reached in practice, and it does not consider other steps in power generation, such as production, transportation and storage of fuel and conversion of the electricity into mechanical power. However, this calculation allows the comparison of different types of power generation.
The maximum theoretical energy efficiency of a fuel cell is 83%, operating at low power density and using pure hydrogen and oxygen as reactants (assuming no heat recapture) According to the World Energy Council, this compares with a maximum theoretical efficiency of 58% for internal combustion engines. While these efficiencies are not approached in most real world applications, high-temperature fuel cells (solid oxide fuel cells or molten carbonate fuel cells) can theoretically be combined with gas turbines to allow stationary fuel cells to come closer to the theoretical limit.
A gas turbine would capture heat from the fuel cell and turn it into mechanical energy to increase the fuel cell’s operational efficiency. This solution has been predicted to increase total efficiency to as much as 70%.
____________________________
In practice
The tank-to-wheel efficiency of a fuel-cell vehicle is greater than 45% at low loads and shows average values of about 36% when a driving cycle like the NEDC (New European Driving Cycle) is used as test procedure. The comparable NEDC value for a Diesel vehicle is 22%. In 2008 Honda released a demonstration fuel cell electric vehicle (the Honda FCX Clarity) with fuel stack claiming a 60% tank-to-wheel efficiency.
It is also important to take losses due to fuel production, transportation, and storage into account. Fuel cell vehicles running on compressed hydrogen may have a power-plant-to-wheel efficiency of 22% if the hydrogen is stored as high-pressure gas, and 17% if it is stored as liquid hydrogen. Fuel cells cannot store energy like a battery, except as hydrogen, but in some applications, such as stand-alone power plants based on discontinuous sources such as solar or wind power, they are combined with electrolyzers and storage systems to form an energy storage system.
Most hydrogen, however, is produced by steam methane reforming, and so most hydrogen production emits carbon dioxide. The overall efficiency (electricity to hydrogen and back to electricity) of such plants (known as round-trip efficiency), using pure hydrogen and pure oxygen can be “from 35 up to 50 percent”, depending on gas density and other conditions. While a much cheaper lead–acid battery might return about 90%, the electrolyzer/fuel cell system can store indefinite quantities of hydrogen, and is therefore better suited for long-term storage.
Solid-oxide fuel cells produce exothermic heat from the recombination of the oxygen and hydrogen. The ceramic can run as hot as 800 degrees Celsius. This heat can be captured and used to heat water in a micro combined heat and power (m-CHP) application. When the heat is captured, total efficiency can reach 80–90% at the unit, but does not consider production and distribution losses. CHP units are being developed today for the European home market.
Professor Jeremy P. Meyers, in the Electrochemical Society journal Interface in 2008, wrote, “While fuel cells are efficient relative to combustion engines, they are not as efficient as batteries, due primarily to the inefficiency of the oxygen reduction reaction (and … the oxygen evolution reaction, should the hydrogen be formed by electrolysis of water)…. [T]hey make the most sense for operation disconnected from the grid, or when fuel can be provided continuously.
For applications that require frequent and relatively rapid start-ups … where zero emissions are a requirement, as in enclosed spaces such as warehouses, and where hydrogen is considered an acceptable reactant, a [PEM fuel cell] is becoming an increasingly attractive choice [if exchanging batteries is inconvenient]”. In 2013 military organizations are evaluating fuel cells to significantly reduce the battery weight carried by soldiers.
______________________________
Power
Stationary fuel cells are used for commercial, industrial and residential primary and backup power generation. Fuel cells are very useful as power sources in remote locations, such as spacecraft, remote weather stations, large parks, communications centers, rural locations including research stations, and in certain military applications. A fuel cell system running on hydrogen can be compact and lightweight, and have no major moving parts. Because fuel cells have no moving parts and do not involve combustion, in ideal conditions they can achieve up to 99.9999% reliability. This equates to less than one minute of downtime in a six-year period.
Since fuel cell electrolyzer systems do not store fuel in themselves, but rather rely on external storage units, they can be successfully applied in large-scale energy storage, rural areas being one example.There are many different types of stationary fuel cells so efficiencies vary, but most are between 40% and 60% energy efficient.
However, when the fuel cell’s waste heat is used to heat a building in a co-generation system this efficiency can increase to 85%.This is significantly more efficient than traditional coal power plants, which are only about one third energy efficient. Assuming production at scale, fuel cells could save 20–40% on energy costs when used in co-generation systems.
They are also much cleaner than traditional power generation; a fuel cell power plant using natural gas as a hydrogen source would create less than one ounce of pollution (other than CO 2) for every 1,000 kW·h produced, compared to 25 pounds of pollutants generated by conventional combustion systems. Fuel Cells also produce 97% less nitrogen oxide emissions than conventional coal-fired power plants.
_____________________________+
Automobiles
Although there are currently no fuel cell vehicles available for commercial sale, over 20 fuel cell electric vehicle (FCEV) prototypes and demonstration cars have been released since 2009. Demonstration models include the Honda FCX Clarity, Toyota FCHV-adv, and Mercedes-Benz F-Cell. As of June 2011 demonstration FCEVs had driven more than 4,800,000 km (3,000,000 mi), with more than 27,000 refuelings.
Demonstration fuel cell vehicles have been produced with “a driving range of more than 400 km (250 mi) between refueling”. They can be refueled in less than 5 minutes. The U.S. Department of Energy’s Fuel Cell Technology Program claims that, as of 2011, fuel cells achieved 53–59% efficiency at one-quarter power and 42–53% vehicle efficiency at full power,and a durability of over 120,000 km (75,000 mi) with less than 10% degradation.
In a Well-to-Wheels simulation analysis, that “did not address the economics and market constraints”, General Motors and its partners estimated that per mile traveled, a fuel cell electric vehicle running on compressed gaseous hydrogen produced from natural gas could use about 40% less energy and emit 45% less greenhouse gasses than an internal combustion vehicle.
A lead engineer from the Department of Energy whose team is testing fuel cell cars said in 2011 that the potential appeal is that “these are full-function vehicles with no limitations on range or refueling rate so they are a direct replacement for any vehicle. For instance, if you drive a full sized SUV and pull a boat up into the mountains, you can do that with this technology and you can’t with current battery-only vehicles, which are more geared toward city driving.”
Some experts believe, however, that fuel cell cars will never become economically competitive with other technologies or that it will take decades for them to become profitable. “Only about 25% of the power generated from wind, water, or sun is converted to practical use.” The study further noted that “Electricity obtained from hydrogen fuel cells appears to be four times as expensive as electricity drawn from the electrical transmission grid. … Because of the high energy losses [hydrogen] cannot compete with electricity.”
Furthermore, the study found: “Natural gas reforming is not a sustainable solution”. “The large amount of energy required to isolate hydrogen from natural compounds (water, natural gas, biomass), package the light gas by compression or liquefaction, transfer the energy carrier to the user, plus the energy lost when it is converted to useful electricity with fuel cells, leaves around 25% for practical use.”
Boeing researchers and industry partners throughout Europe conducted experimental flight tests in February 2008 of a manned airplane powered only by a fuel cell and lightweight batteries. The fuel cell demonstrator airplane, as it was called, used a proton exchange membrane (PEM) fuel cell/lithium-ion battery hybrid system to power an electric motor, which was coupled to a conventional propeller.
In 2003, the world’s first propeller-driven airplane to be powered entirely by a fuel cell was flown. The fuel cell was a unique FlatStackTM stack design, which allowed the fuel cell to be integrated with the aerodynamic surfaces of the plane.
There have been several fuel-cell-powered unmanned aerial vehicles (UAV). A Horizon fuel cell UAV set the record distance flown for a small UAV in 2007. The military is especially interested in this application because of the low noise, low thermal signature and ability to attain high altitude. In 2009 the Naval Research Laboratory’s (NRL’s) Ion Tiger utilized a hydrogen-powered fuel cell and flew for 23 hours and 17 minutes.
________________________
Boats
The world’s first fuel-cell boat HYDRA used an AFC system with 6.5 kW net output. Iceland has committed to converting its vast fishing fleet to use fuel cells to provide auxiliary power by 2015 and, eventually, to provide primary power in its boats. Amsterdam recently introduced its first fuel-cell-powered boat that ferries people around the city’s famous and beautiful canals.
Submarines
The Type 212 submarines of the German and Italian navies use fuel cells to remain submerged for weeks without the need to surface.
The U212A is a non-nuclear submarine developed by German naval shipyard Howaldtswerke Deutsche Werft. The system consists of nine PEM fuel cells, providing between 30 kW and 50 kW each. The ship is silent giving it an advantage in the detection of other submarines. A Recent naval paper has theorized about the the possibility of a Nuclear-Fuel Cell Hybrid whereby the fuel cell is used when silent operations are required and then replenished from the Nuclear reactor (and water). Such a system could potentially give a submarine weeks of stealth capability at a time with the endurance of a Nuclear reactor. It is not known if any such submarines have been built.
______________________________________
ATTENTION READERS
We See The World From All Sides and Want YOU To Be Fully InformedIn fact, intentional disinformation is a disgraceful scourge in media today. So to assuage any possible errant incorrect information posted herein, we strongly encourage you to seek corroboration from other non-VT sources before forming an educated opinion.
About VT - Policies & Disclosures - Comment Policy